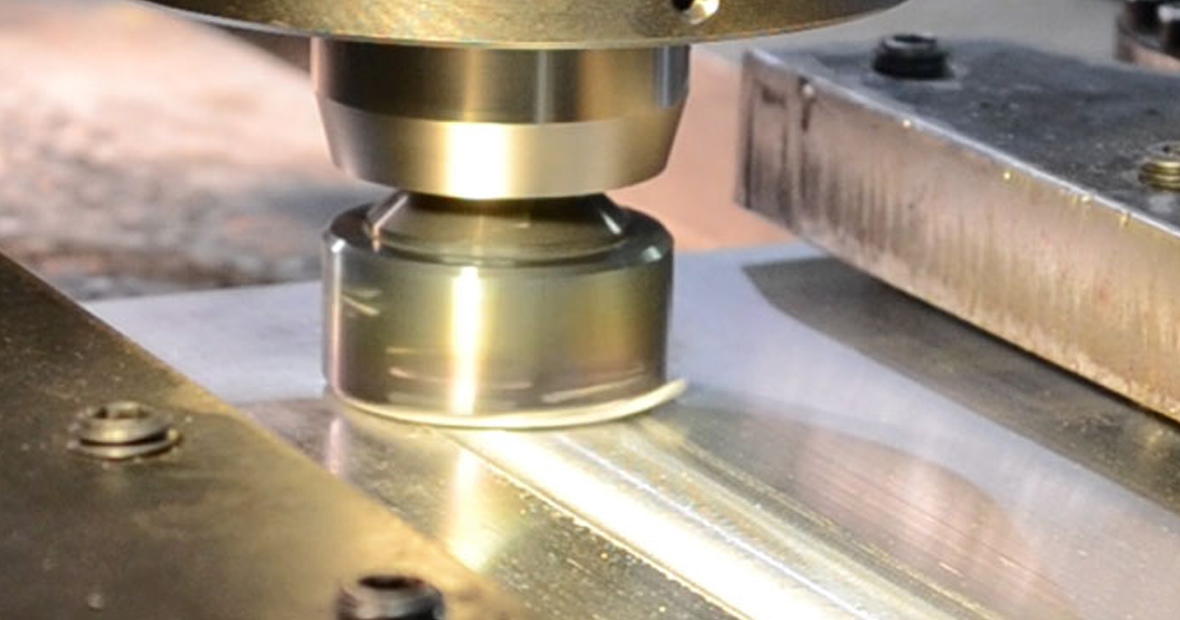
Braving the heat and molten metal, operators of friction stir welding (fsw) machinery face potential hazards daily. A commitment to safety protocols and practices becomes paramount in this high-risk environment. The focus of this discussion lies on the meticulous safety procedures for fsw operators. Delving into the creation of exhaustive safety manuals, the necessity of regular audits, and the crucial role of constant education and supervision, this topic seeks to emphasize the importance of each element. The discussion then transitions to the critical role of Personal Protective Equipment (PPE) in fsw, followed by an examination of the maintenance and safety checks required for these machines. Lastly, the spotlight is directed towards emergency procedures and managing risks within fsw operations.
Key safety protocols for fsw operators
Under the broad category of friction stir welding (FSW) machine safety, the emphasis on protocols and practices for operator protection cannot be overemphasized. FSW, a solid-state joining process, presents unique safety challenges that necessitate the development of comprehensive safety manuals. These manuals, tailored to the FSW processes, ensure operators' health and safety by providing detailed procedures for risk management and the use of appropriate personal protective equipment (PPE).
Developing Comprehensive Safety Manuals for FSW Processes
Given the industry-specific risks associated with FSW, implementing safety protocols aimed at minimizing accidents is paramount. Certified and continuous training in FSW is vital for an in-depth understanding of these safety procedures. Safety manuals offer guidance on the use of PPE, which is integral to operator protection during FSW operations.
Regular Safety Audits and Compliance Checks in FSW Operations
Another aspect of enhancing FSW safety is the conduct of regular safety audits and compliance checks. These serve to reinforce a safety culture within the FSW industry. Audits and feedback loops help to identify potential risks and ensure adherence to safety protocols.
Role of Supervision and Continuous Education in Enhancing FSW Safety
Supervision and continuous education play a crucial role in FSW safety. Supervision ensures that safety procedures are followed, while continuous education keeps operators abreast of new safety protocols and industry developments. Furthermore, the establishment of emergency and first aid procedures specific to FSW-related risks is a key component in any comprehensive safety plan.
Preventive maintenance of FSW machines is another factor that significantly contributes to the safe operation of the welding process. Proper maintenance helps prevent machine failures that could compromise safety. Overall, the importance of safety in the FSW industry cannot be overstated, and it is the shared responsibility of machine manufacturers, supervisors, and operators alike to uphold these safety standards.
Personal protective equipment (ppe) for friction stir welding
For the purpose of mitigating potential health hazards, the use of specific Personal Protective Equipment (PPE) during the operation of a Friction stir welding machine is vital. PPE plays a significant role in preventing injuries and ensuring operator safety. A proper fit and correct usage of PPE is essential to maximize the protection against risks associated with friction stir welding.
Periodic maintenance and replacement of PPE are indispensable practices to maintain constant and efficient protection. Analyzing health risks related to friction stir welding and choosing the right PPE for each potential hazard is a fundamental aspect of safety protocols. Constant awareness about technological advancements and innovations in PPE can significantly enhance the safety of friction stir welding operators. Safety training and education strategies highlighting the importance of accident prevention are imperative for operators.
Machine maintenance and safety checks in fsw
Regular inspections hold significant weight in the sphere of Friction Stir Welding (FSW) machine maintenance. Crafting a preventive maintenance schedule for these specialized machines presents a proactive approach to ensuring optimal performance and longevity. Each use of FSW machines necessitates preliminary safety checks, establishing a protocol that confirms all safety systems are functioning as designed.
Further augmenting the safety measures, lockout/tagout procedures have paramount importance during maintenance and repair operations. These procedures offer a safeguard for technicians, preventing unexpected equipment activation. Potential risks associated with FSW machine usage require careful evaluation, a process which allows for identification and reduction of potential hazards to operators. Training operators on FSW-specific safety practices emphasizes the correct and secure use of equipment.
Environmental control around FSW machines plays a pivotal role, maintaining a workplace that is both safe and adheres to safety standards. The role of environmental control is not limited to the immediate surroundings of the machines, but extends to the broader workspace, ensuring an atmosphere conducive to safe and efficient operation of the equipment.
Emergency procedures and risk management in fsw operations
In the realm of Friction Stir Welding (FSW), operator protection remains a priority.
are critical factors in ensuring workplace safety. The significance of ongoing training and emergency simulations for FSW operators cannot be understated. These initiatives equip them with necessary skills to respond to unforeseen circumstances.
Crucial to FSW operations is the establishment and implementation of a FSW-specific evacuation plan. This plan should be clear, accessible, and well-understood by all operators. Regular maintenance and use of Personal Protective Equipment (PPE) is another vital aspect of FSW operations, aiding in the prevention of workplace accidents.
In the event of a FSW machine failure, operators need to follow established procedures to minimize risks. Identifying and managing health risks linked to fumes and particles emitted during FSW welding is another key aspect of maintaining a safe work environment. Finally, controlling electrical risks associated with the use of FSW machines is a crucial component of risk management. All these measures contribute significantly to overall safety and health control in FSW operations.